Tracking the Productivity of Rental Equipment
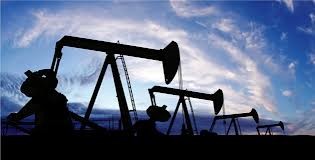
A common approach in the construction business for measuring productivity is to calculate the firm’s output in dollars and divide it by the total number of hours assigned to the labor behind it.
Often, although it’s crucial to include rental hours to gauge an accurate productivity outcomes, the operational costs of machinery and equipment are overlooked, making the productivity measurement inaccurate.
Studies conducted by the top equipment manufacturers indicate that contractors generally receive about 800 to 900 productive hours from their equipment annually, compared to a 50% productivity level from workers during an 8-hour work day. Basically, that means a lot of time is spent on the site waiting for material or subs to finish their work.
One way to track the productivity of rental equipment is to use the Sage software suite to record hours used per assigned task. Sage can also make note of when equipment is in a standby status and, to get the total productivity picture, keep track of non-productive tasks, such as unassigned jobs of minimal value to the project.
Ultimately, the Sage software will collect enough data to indicate how effectively rental equipment is being used as a percentage of the entire project. In addition, the use of an inventory control software like Sage will aid in parts replacement and maintenance schedules for long-term equipment rentals in addition to offering cloud access and storage. Finally, Sage software can also help tie together the various cost profiles and help you achieve better productivity.
Contact Asyma Solutions Ltd. for more information.